Preventive Maintenance Software
FastMaint CMMS - the easiest way to plan, track & optimize maintenance
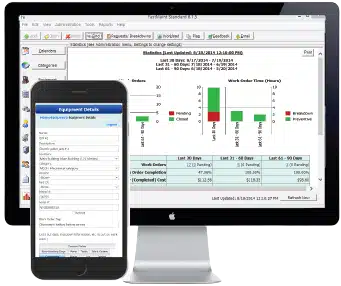
Used By
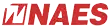
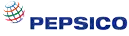
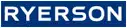
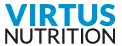
FastMaint Preventive Maintenance Software Benefits
- Preventive maintenance program that is simple to use & setup
- For PM jobs as well as corrective work at commercial & industrial facilities
- Import equipment, facilities, spare parts from Excel spreadsheets for fast setup
- Schedule jobs by dates, meter readings, alarms and more
- Standalone system. Targeted at the needs of small to mid-size maintenance departments
- From $2000 (one-time, download) or from $100/ month cloud subscription
(Download or Cloud CMMS)
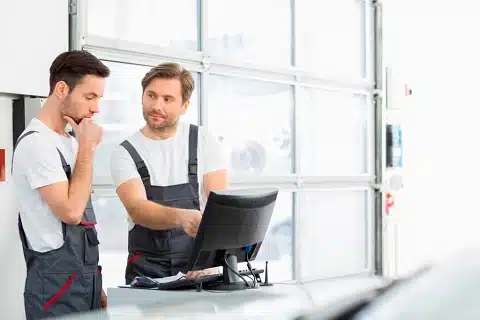
Preventive Maintenance Software Features
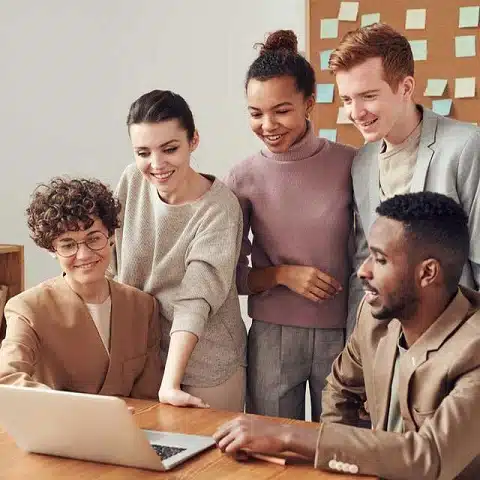
Who it is for
Maintenance managers will like the combined management of equipment & facilities. Easily create corrective and preventive maintenance plans for all these assets. A great solution for manufacturing & industrial operations, commercial facilities like warehouses, office complexes, resorts and more. Maintenance work order management is made easier. In addition, built in parts inventory management & purchasing. Track parts & supplies use & availability. Reduce repair delays due to items being out of stock.
Variety of job scheduling options
Create & schedule all types of jobs with the same program interface. Schedule preventive maintenance tasks on equipment by time (for instance every five weeks), or by an alarm condition, or by meter readings on the equipment (for example every 6,000 miles) and so on. In addition schedule unplanned maintenance activities due to equipment breakdowns as needed.
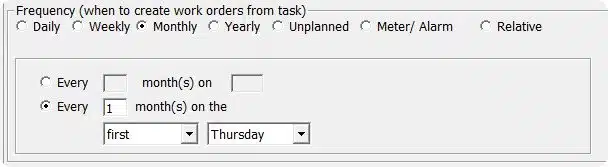
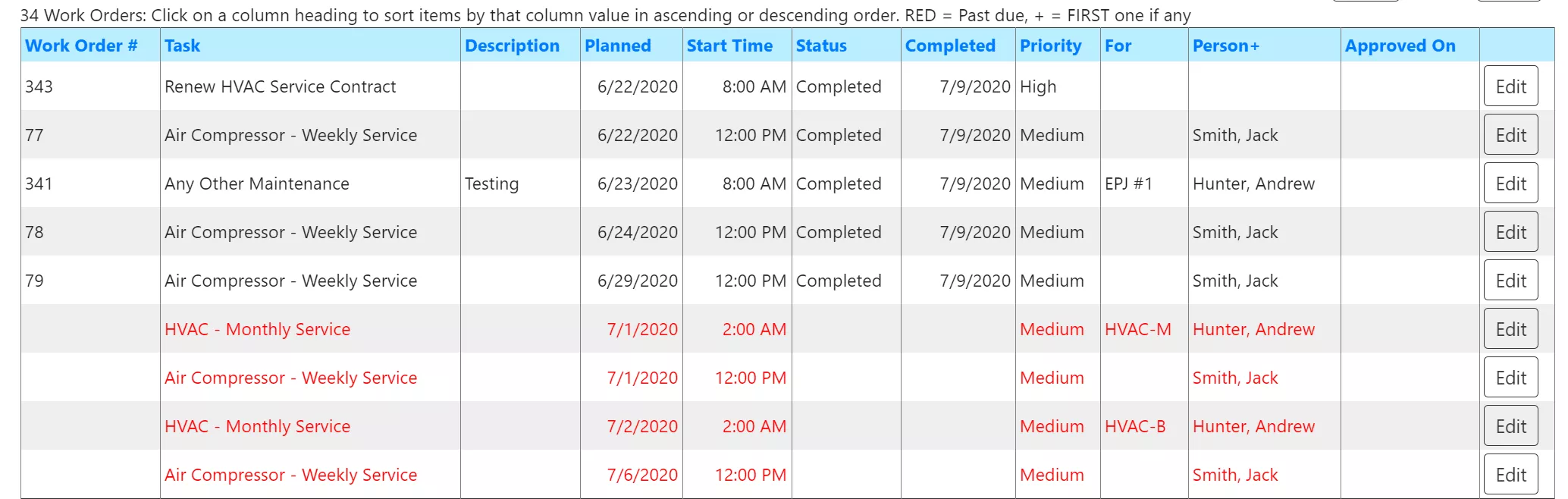
List of maintenance work orders showing current state
Track pending work that may be missed
Use work orders to schedule & track jobs to be done by maintenance team technicians or sub-contractors. Work orders can printed or emailed with reminders sent out when they are overdue. In addition, print maintenance information such as pictures and detailed instructions on work orders. Above all this helps the maintenance team perform maintenance activities correctly and reduces rework.
Import & setup from Excel data
For instance, do you already have much of your data in Excel spreadsheets? You can import equipment, locations, spare parts, job templates and more.
Use the Import feature to get a step-by-step wizard that guides you to map your data to the correct fields.
Therefore, you can quickly setup your CMMS solution and get going.
Plus, you can export data to Excel files. For instance last quarter’s work orders for further analysis.
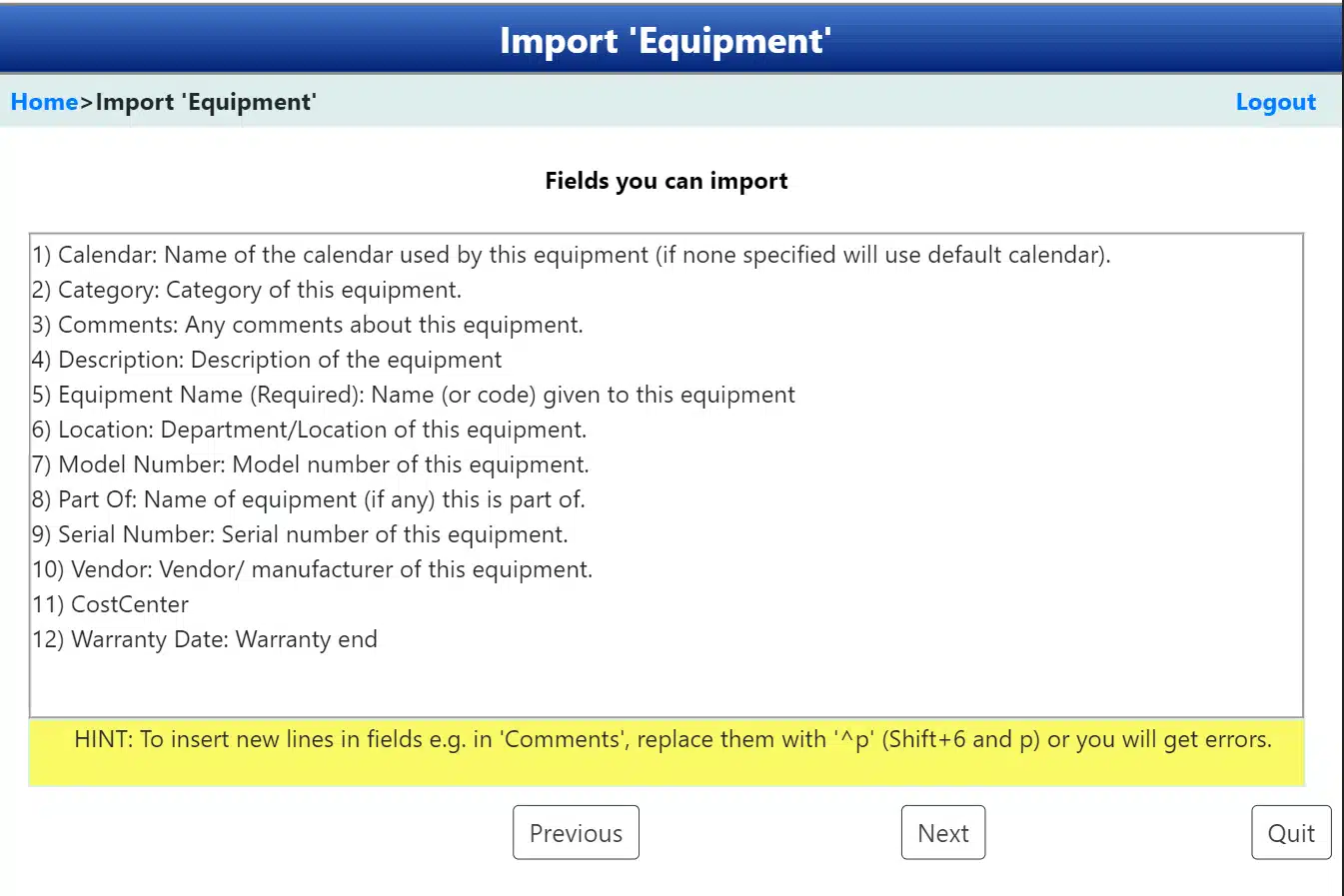
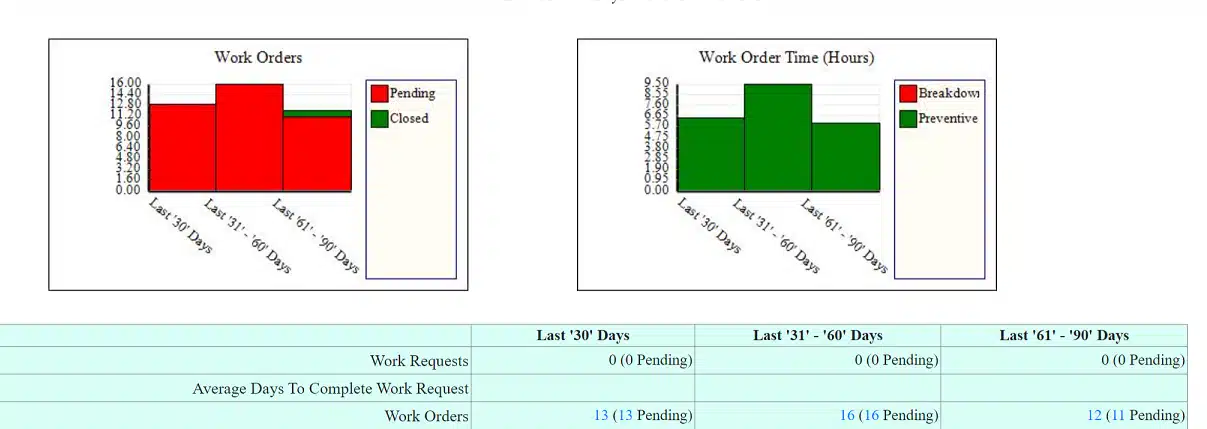
Variety of reports & analytics
FastMaint has a variety of reports that you can email or print. Maintenance history is at your fingertips. Therefore, you can get an idea of work order costs, usage of spare parts, equipment downtime, asset performance and more. Above all, use the one-page Statistics report to get an idea of your current situation at a glance!
Customize or create new reports with the WYSIWYG Report Editor. For instance insert custom fields, change report formats, add your logos and so on.
Preventive Maintenance Software For
Preventive Maintenance Tips From Our Blog
Certainly preventive maintenance is a critical function of a maintenance department! The equipment and machines used for production are a manufacturing or industrial operation’s lifeblood. Equipment shutdowns means products not being made or delivered to customers.
Have you ever had this happen to you?
read more
Proactive maintenance tries to identify and fix the root causes equipment failures. Therefore, as part of your maintenance plan it can result in significant cost savings. It is different from reactive maintenance and preventive maintenance.
Preventive maintenance vs. proactive maintenance: Preventive maintenance will try to perform repairs or parts replacement based on a maintenance schedule. For example an oil change every week, change a gasket every 1000 run-hours and so on.
On the other hand …
read more
Preventive maintenance scheduling leading to complaints?!
It does sound weird!
Have you ever had this happen to you?
For example, management or other departments complain that your preventive maintenance scheduling is too much. Maybe equipment is frequently unavailable because of scheduled preventive maintenance. In addition your team complains that they spend too much time checking equipment and doing preventative maintenance chores.
Depending on your work order backlog and who is complaining, you should take these complaints seriously or not!
read more
When you have several hundred equipment it can be hard to get an idea of preventive maintenance that is due for all the different equipment. Hence, this is where reports from your CMMS software can be quite helpful. For instance, you may find a report called Equipment Maintenance Calendar. Use it to get an idea of preventative work due in the coming months week by week.
read more
Maintenance managers are acutely aware of how CMMS software aka maintenance software can improve maintenance operations and reduce expenses. However, it can be difficult to get support from senior management or business owners to buy such software and put it to use.
Have you ever had this happen to you?
On the other hand…
From management’s point of view, there are several other areas besides maintenance software where such capital expenditures can be made. Nearly all of these can also improve business operations.
So how do we justify putting limited budget dollars to get maintenance software versus spending it elsewhere?
When your organization buys a CMMS/ maintenance software program one of your first challenges will be how to set up & use your new system. Your IT department or consultants can install and do some initial set up the system for you. However, the maintenance planner or maintenance manager have to decide how to setup and use the system!
Have you ever had this happen to you?😒
You will need to find some way to start using the system without bogging down or slowing maintenance operations. After all the critical job here is ongoing equipment & facility maintenance.
Just think about it…
The maintenance management software is just a tool. It should not hold up or delay maintenance work because it needs to be set up or it has a complicated workflow.
So how can we do this with a minimum of disruption?
read more
Scheduling preventative maintenance (PM) is a frequently overlooked aspect of maintenance management. Certainly, nearly every equipment needs some kind of regular maintenance. Above all, this reduces the chance of unexpected failure or repetitive breakdowns. Equipment downtime results in big costs due to lost production, variable product quality and poor customer satisfaction.
read more