Facilities Maintenance Software
FastMaint CMMS - the easiest way to plan, track & optimize maintenance
No credit card required
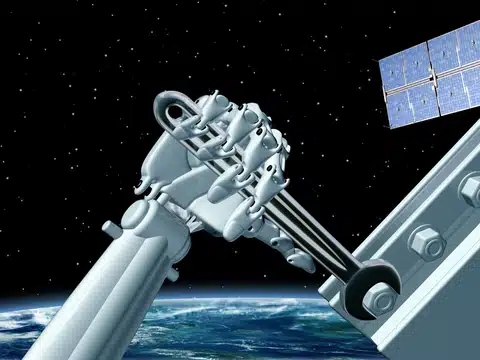
Used By
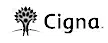
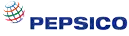
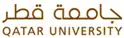
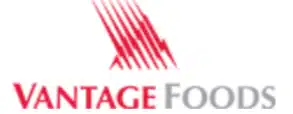
Why Facility Managers Like FastMaint CMMS Software
- Manage unplanned (breakdown) & planned (preventive) jobs
- Stand-alone FM software. Suited for small to mid-size teams
- Fast setup. Import facilities, equipment, tasks and more from Excel spreadsheets
- Identify missed work, reduce breakdown/ emergency work
- Inventory management, vendors, re-ordering & purchasing
- One-time fee (installed onsite) or monthly subscription (Cloud CMMS)
(Download or Cloud CMMS)
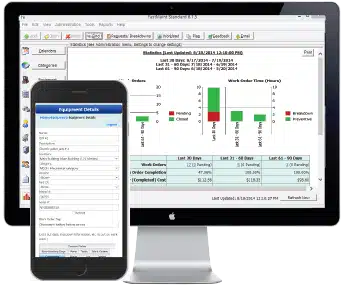
FastMaint CMMS Facilities Maintenance Software – Essential Features
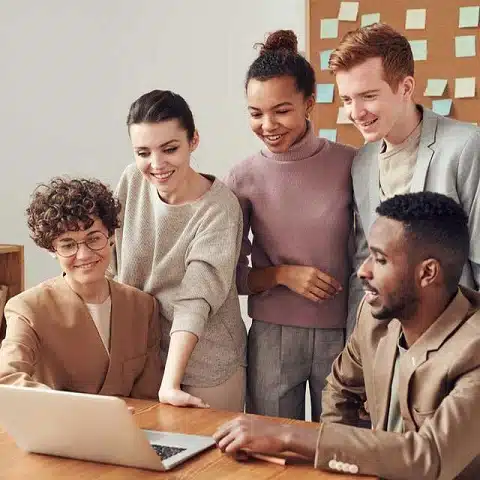
Who will benefit
Facilities managers will like the combined maintenance tracking of equipment & facilities. Easily create & manage corrective and preventive maintenance schedules. Useful at a variety of industrial & commercial facilities like manufacturing plants, warehouses, office complexes, hotels, resorts and more. Reduce out of stock situations by tracking parts used and inventory availability. In addition, create & manage purchase orders. In conclusion, what you need to make facilities management easier.
Fast setup – import from Excel files
Have a lot of existing data in Excel files? You can import spare parts, equipment, locations, job templates, and more. Hence, you can quickly setup your system and get going.
The Import function comes with a a step-by-step wizard to guide you. This makes it easier to copy your data to the correct fields.
In addition, export data to Excel files. For instance, you can export last month’s work orders. This will allow for further analysis or import into other systems.
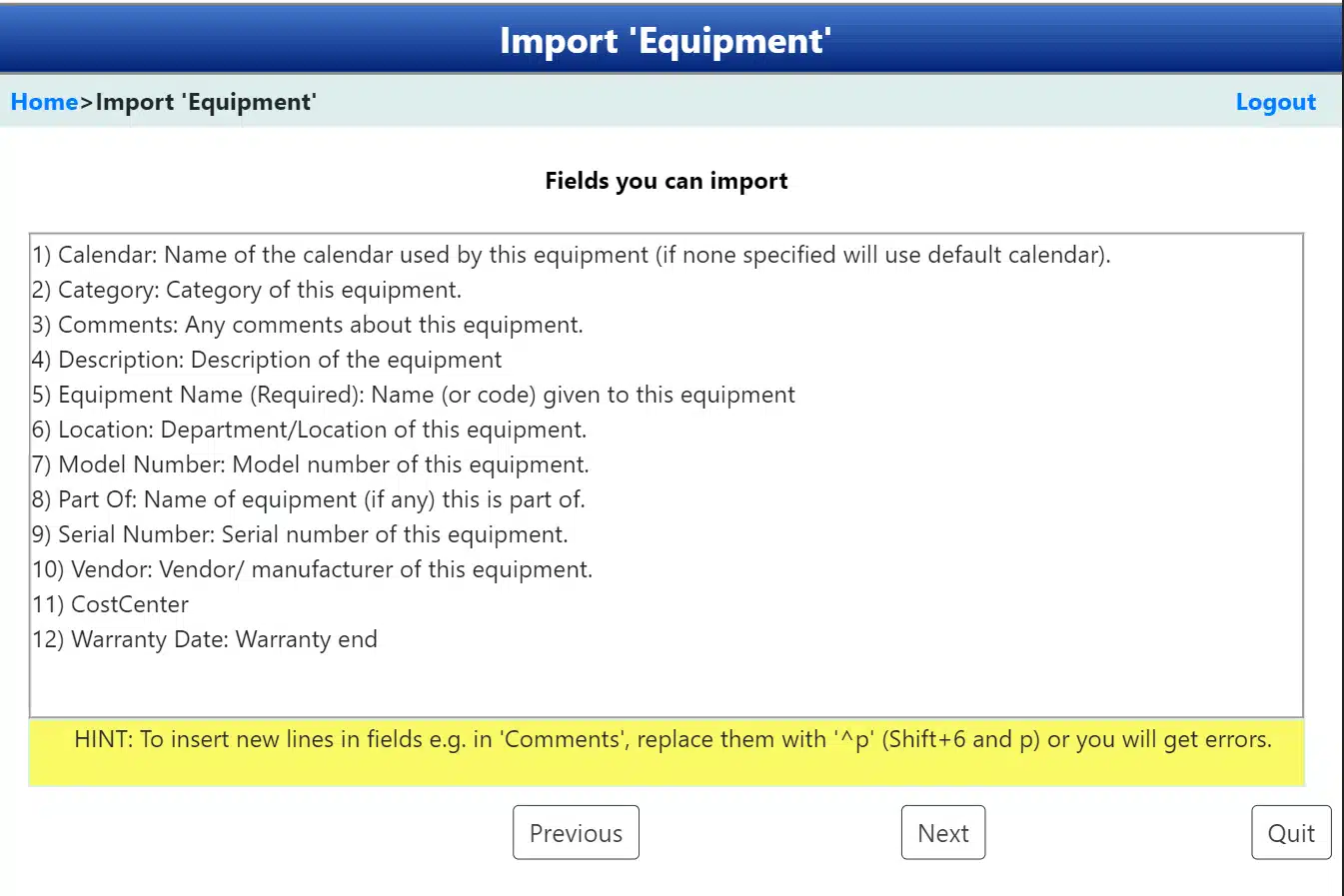
Import equipment from Excel spreadsheet
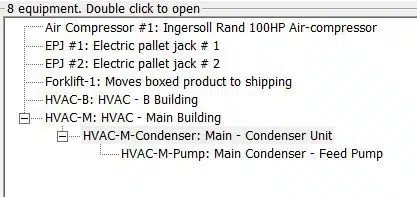
Create a facilities hierarchy for easier maintenance
Set up relationships between locations & equipment
Create a hierarchy of locations or equipment. Subsequently use this to manage them, create roll-up reports, etc. For instance, expand an equipment and find all sub-equipment that are part of it.
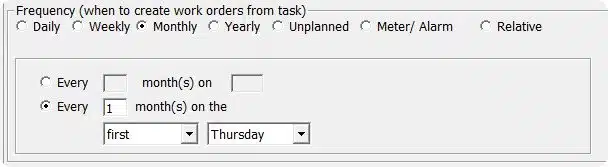
Set a maintenance job frequency
Capable job scheduling features
Schedule & track all types of maintenance jobs with the same simple program interface. Schedule & manage preventive maintenance by alarms, meter readings on the equipment (say every 3,000 miles) or by time (say every three weeks) and so on. In addition, manage & track corrective work due to equipment breakdowns.
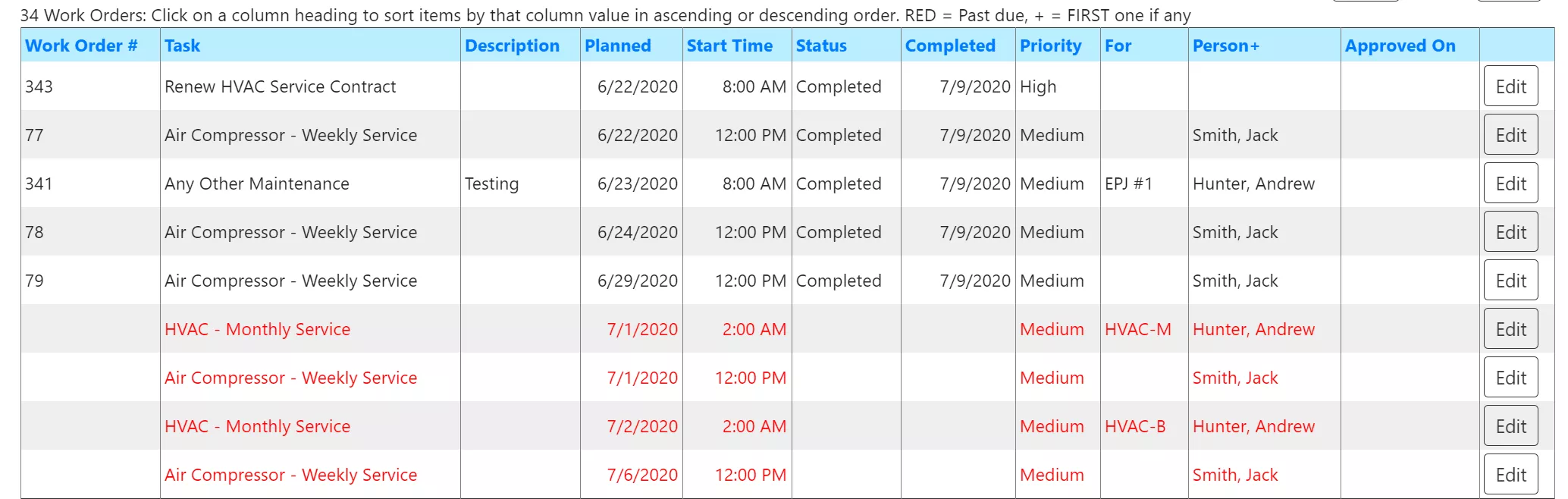
Work order list showing job status
Tracking of pending work & work order management
Use work orders to schedule & track work being done by technicians or outside sub-contractors. Work orders can printed or emailed with reminders sent out when they are overdue. In addition, print pictures and detailed instructions on work orders to help technicians perform maintenance jobs correctly.
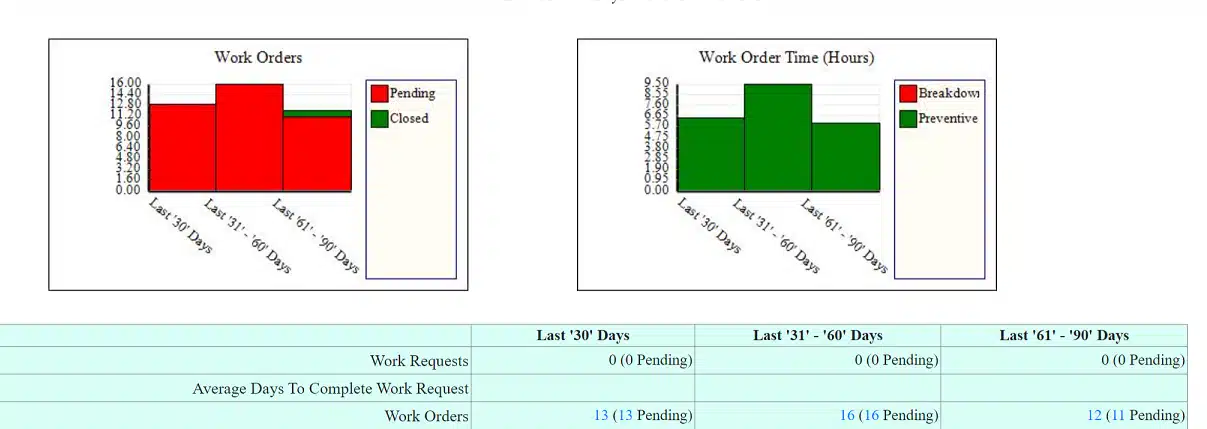
Many useful reports & analytics
You can get many different reports that can printed or emailed. So you can get an idea of equipment downtime, work order costs, spare parts usage and more. Above all, use the one-page Statistics report to get an idea of your current situation at a glance!
Use the WYSIWYG Report Editor to create your own reports and graphs. Or customize existing reports to your needs. For instance, you can add your own logos, change report formats, print custom fields and more.
More Facility Maintenance Tips From Our Blog
Maintenance management covers a wide area since regular maintenance is required for a variety of assets. A CMMS software program is not only useful in locations with a lot of machines (e.g. manufacturing plants, mining operations, etc.) but useful where you have a lot of facilities needing maintenance (hotel, resorts, restaurants) as well as those with other equipment (e.g. utilities, vehicle fleets).
read more
Having a lot of equipment breakdowns & unexpected downtime? Or is everything under control and there are hardly any maintenance emergencies? 😎Wow!
Whatever the situation, operations managers and maintenance managers need to regularly identify problem equipment. These bad boys are the ones that cause frequent shutdowns or incur big maintenance costs.
When you lots of equipment it can be hard to do!
read more
Maintenance backlog refers to maintenance work that is overdue. In other words, it shows the total time estimate it would take to complete the pending maintenance work orders. Maintenance backlog is normally measured in hours or days. Above all it is a very important maintenance metric for facilities managers, maintenance managers and maintenance planners.
Big increases in maintenance backlog should be taken seriously!
read more
Maintenance request software may seem like a rather specialized requirement! However, if one is responsible for managing maintenance at a large facility or industrial plant we will be handling a lot of requests for maintenance work.
Most requests will be for emergency or breakdown maintenance. Often the requester wants an immediate fix! This is especially true when equipment & building systems are not working as expected.
But that’s just part of the story…
read more
Do you have a lot of equipment to maintain? Is reactive maintenance aka breakdown maintenance dominating your day? 🙁 Want to create a good preventive maintenance plan to reduce equipment breakdowns and complaints from users and management?
When you have to manage maintenance on many equipment you really must use a maintenance Maintenance managers are acutely aware of how CMMS software aka maintenance software can improve maintenance operations and reduce expenses. However, it can be difficult to get support from senior management or business owners to buy such software and put it to use.
Have you ever had this happen to you?
On the other hand…
read more