Industrial Plant Maintenance Software
FastMaint CMMS software for manufacturing & process industries. Powerful & easy to use
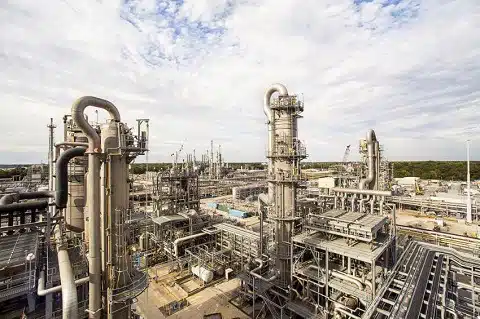
Some customers
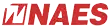
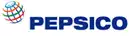
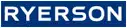
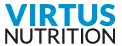
Industrial Plant Maintenance System With FastMaint CMMS
- Import equipment, facilities, spare parts and more from Excel spreadsheets for fast setup
- Create maintenance checklists, corrective & preventive maintenance plans
- Receive & track maintenance work requests from machine operators
- Manage equipment, assembly lines, facilities, spares, purchases and more
- Stand-alone program. Great for small to mid-size teams
- For manufacturing plants, power plants, process industries
- Run on your computer (one time fee). Or use cloud CMMS (monthly fee)
(Download or Cloud CMMS)
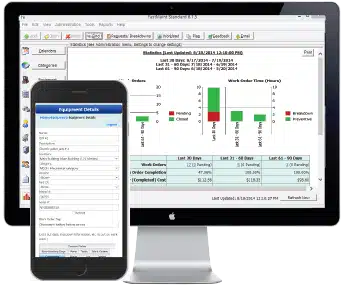
FastMaint CMMS Plant Maintenance Software Features
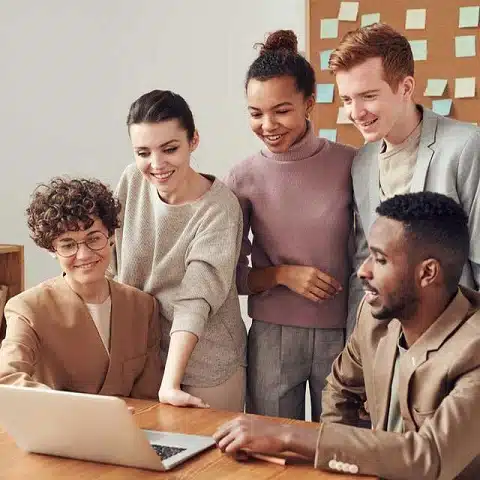

Built for industrial & manufacturing plants
Maintenance managers can easily create corrective and preventive maintenance plans & maintenance checklists for machinery, other equipment & facilities. Create equipment hierarchies. Define process or manufacturing assembly lines and sub-equipment.
Track asset maintenance costs by equipment, department & location. Likewise see how much materials and labor is costing you. Available as stand alone, networked or cloud editions.
Great for industrial plants of all types for instance manufacturing products, process industries (such as refineries, chemicals), power plants and more.

Maintenance scheduling is easy!
FastMaint has a single interface to plan & schedule different types of maintenance jobs.
For instance, schedule unplanned maintenance from a task library when an equipment breaks down.
Similarly schedule preventive or planned maintenance from a library of preventive maintenance jobs you create.
You can plan maintenance work on equipment by time – say every four months. Or by change in meter readings on the equipment – say after every 300 units produced. Or when an alarm is reported. Or when another maintenance task is completed and so on.
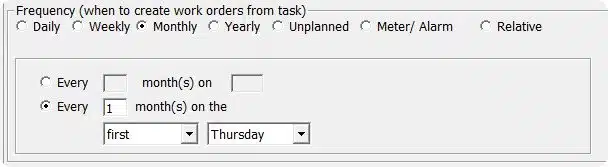
Example maintenance task to be done monthly
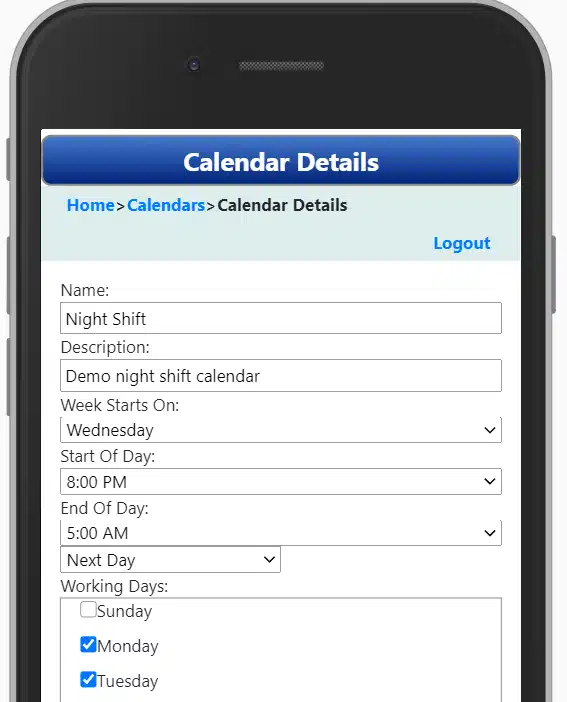

Calendars for maintenance work – avoid conflicts
Define different maintenance work calendars to schedule maintenance, adjust equipment run times and so on. For example have a calendar for regular working days, another for the 2nd shift, a third for the night shift and a fourth just for plant shutdown days.
With these work calendars, automatically adjust work schedule dates because of holidays and off days. Identify schedule conflicts. See if maintenance personnel will be on holiday when work is scheduled. Associate calendars with machinery to track run-hours and usage to schedule preventive maintenance.
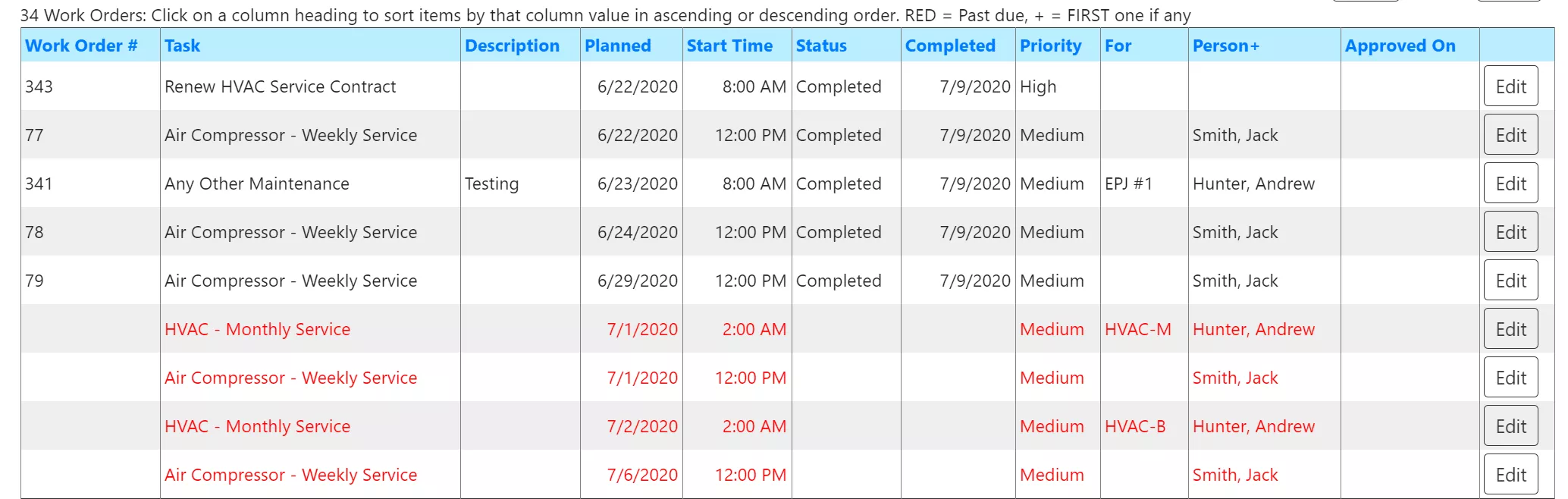

Keep track of maintenance work orders – avoid forgetting them
Based on the schedule in the task templates FastMaint creates work orders for the maintenance work. Maintenance technicians or outside sub-contractors can receive these work orders to complete the jobs. Print the work orders or email them out and send reminders when they are past due. In addition reduce maintenance completion errors by printing pictures and detailed instructions on work orders.
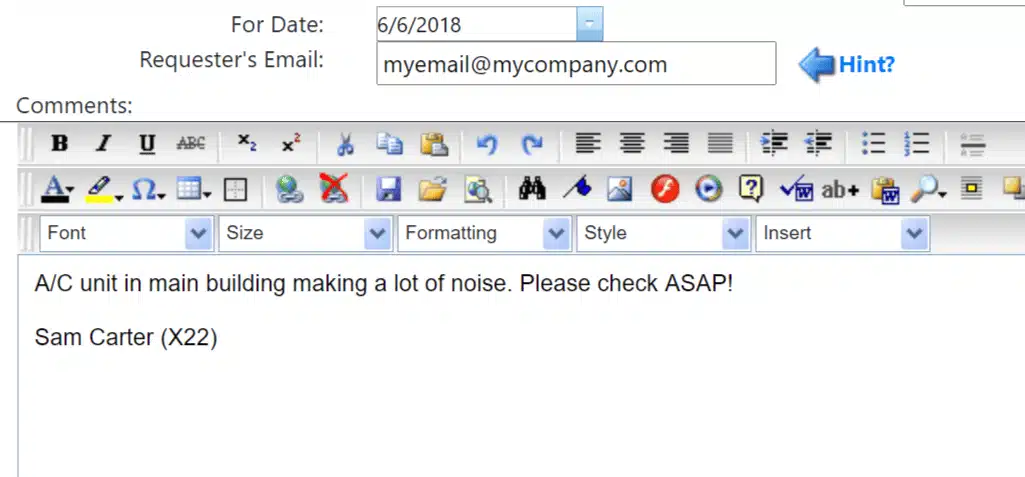

Handle maintenance requests – less tension, faster turnaround
Machine operators or other departments can send you maintenance work requests. So you can receive & keep track of such maintenance requests.
In addition, they can even submit requests for work by email. Therefore requesters do not need to setup anything or need access to FastMaint! Moreover, maintenance requesters can get updates on their maintenance request status by email. You can also email them back for additional information.
Maintenance managers can review these maintenance requests, create work orders from them or cancel them.
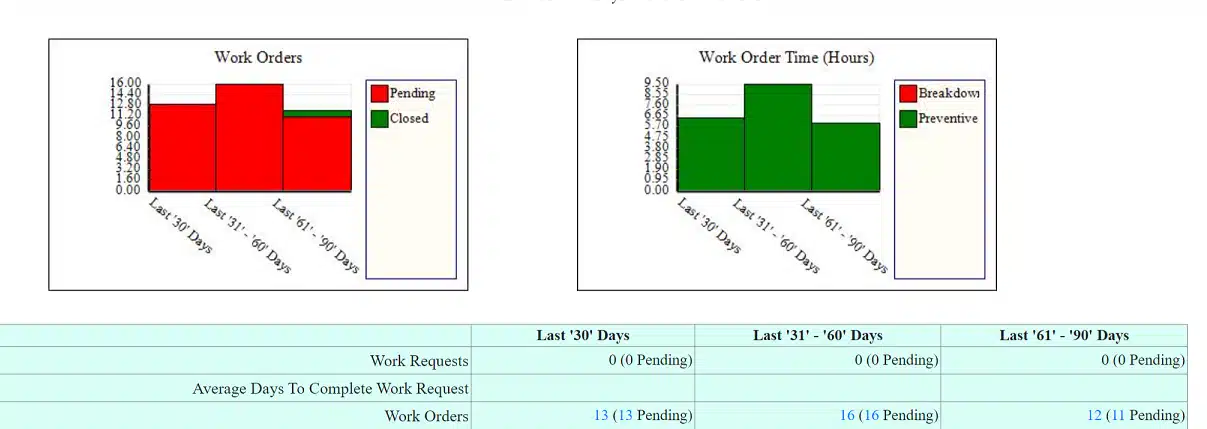

Analytics & customizable reports – find problems faster
FastMaint offers many different reports that can be printed or emailed. These reports will give you an idea of maintenance work costs, usage of spares and supplies, equipment downtime and so on. For instance, the one-page Statistics report will give you an idea of your current maintenance situation at a glance.
Most reports can be customized to your specific format. Create your own reports and graphs with the help of the WYSIWYG Report Editor. For example add custom fields, company logos, graphs and so on.

Faster setup with Excel data imports – less data entry
Already have a lot of data in an Excel spreadsheets or comma delimited files? You can import much of this into the system for faster setup. Import equipment, maintenance spares, job instructions and so on. Hence, this makes it easier for you to get started.
Use the helpful step-by-step wizard in the Import function to guide you to map your data to the correct fields. Did you make any mistakes? You can run the import again to update the data with your corrections!
You can also export data to Excel. For instance last quarter’s work orders for more analysis.
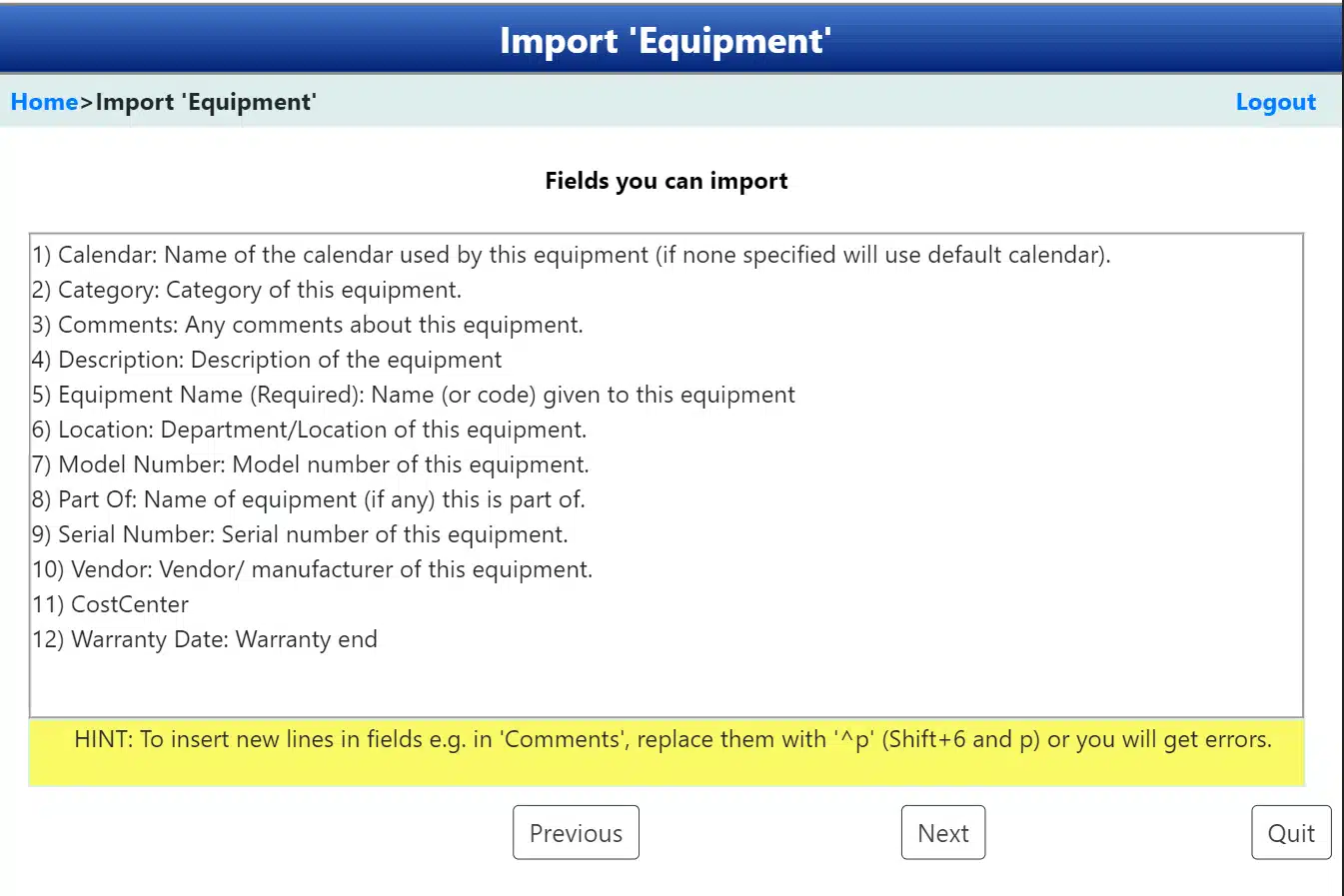
Plant Maintenance Software Selection Advice From Our Blog
Unfortunately in many manufacturing companies big and small there is a tendency in higher management to see maintenance as a not very important but necessary evil. It is really not something they wish to deal with. So they often see the maintenance team not as a crucial part of the organization. Therefore this often results in bad decisions being made for the maintenance team!
CMMS software gets selected on how nice it looks (beautiful and extensive reports are always welcome!). Or how well it integrates with other software (ERP, financial and so on) rather than functionality that will help the maintenance team.
read more
Maintenance management covers a wide area because regular maintenance is required for a variety of assets. Therefore a maintenance management program is not only useful in locations with a lot of machines (e.g. manufacturing plants, mining operations, etc.). It is also useful where you have a lot of facilities needing maintenance (hotel, resorts, restaurants) as well as those with other equipment (e.g. utilities, vehicle fleets).
read more
Equipment maintenance costs at many organizations can be a significant expense. As a result, maintenance managers or supervisors will often be under pressure to reduce these costs. Due to its impact on the bottom line, senior management will also take interest in such cost reductions.
Have you ever had this happen to you?
read more
Most importantly as an operations or maintenance manager you need to regularly identify problem equipment. To clarify these cause frequent shutdowns or incur big maintenance costs. For this Equipment Breakdown reports can be especially useful when you have hundreds of equipment.
read more
Do you have a lot of equipment to maintain? Is reactive maintenance aka breakdown maintenance dominating your day 🙁? Want to create a good preventive maintenance plan to reduce equipment breakdowns and complaints from users and management? Here are a few preventive maintenance planning tips to help you reach those goals.
read more