Essential Maintenance Metrics Every Planner Needs to Know
Get Free Guide
What is maintenance backlog?
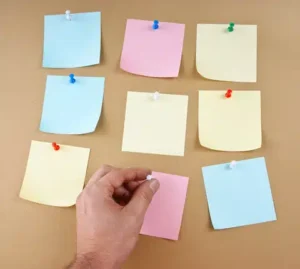
Maintenance backlog refers to maintenance work that is overdue. We usually measure maintenance backlog in hours or days. It shows the total time estimate it would take to complete the pending maintenance work orders. It is a very important maintenance metric for facilities managers, maintenance managers and maintenance planners.
We must take big increases in maintenance backlog seriously!
What causes maintenance backlog?
Maintenance work orders can remain incomplete for a variety of reasons such as:
1. Spare parts or supplies are not available
We can usually forecast in advance spares & supplies required if these are preventive maintenance work orders. For this we can use the maintenance work order reports for future periods in our CMMS software. Use previous unplanned or breakdown work orders to identify equipment that breaks down frequently. We can also find the spare parts & supplies that need to be available so that work can be completed in time.
Keep track of good vendors for parts and supplies. We try to have alternative vendors for them so that we have other vendors to go to in case of supply problems. See the vendor management tips in “6 Ways CMMS/ Maintenance Software Can Improve Vendor Management” for more information.
2. Maintenance technicians (with required skills) not available
This can happen when equipment needs special skills to fix or troubleshoot. The technicians with those skills are too busy or not available because of sickness, vacation or other work. If this is infrequent we can probably manage this. If it happens often we should try train other technicians with these skills so that they can do the job as needed.
3. Equipment problems that need fixes by vendor or outside specialist
While similar to technicians not being available, this is something we have less control over. If this happens often to certain equipment, try to escalate the issues with equipment vendors so that they will send help faster. It can make sense to replace equipment because it is too old or can be replaced with more reliable equipment. The article “Equipment/ Machine Downtime Tracking Analysis Tips” shows ways to do this analysis.
4. Task dropped because a higher priority task came up
This is something that can happen often. In our “Maintenance Management – Tips For Success” e-booklet we recommend organizing a schedule where we can drop lower priority tasks when high priority unplanned or breakdown tasks come up. For such dropped tasks we should try to catch up when we can. We must make sure that they get completed in a reasonable time period or cancel them if no longer required.
5. Work order no longer needed
For example we may have a monthly preventive maintenance check where we replace a filter. The equipment breaks down just before this check is due. As part of the service the technician replaces the filter and does the other steps in the preventive maintenance check. So we no longer need to do the check this month.
Another reason may be that the equipment on which the work is scheduled is no longer in service. Or is out of service for other reasons. In such cases we need to cancel these unneeded work orders.
6. Unable to get access to the equipment/ location because it is in use
We may be unable to complete work because another department (for example Operations) is using the equipment and cannot afford to have it shut down for maintenance. If this is critical maintenance that is being delayed, we need to escalate this to management because such delayed maintenance may result in premature equipment failures. The maintenance department will most likely take the blame!
We can use something like the Equipment Calendar Report to identify and schedule maintenance with other departments. This will reduce such missed work. See the article “Equipment Maintenance Calendars & Scheduling Preventive Maintenance” for more information.
7. Someone forgot about it!
This can happen more often than not especially when we have many work orders to track. This is where CMMS software can be really useful. It can help one keep track of missed maintenance as well as give us reminders as needed.
Track your maintenance backlog
It is critical to have a way to track maintenance backlog. Ideally over time maintenance backlog should decrease. But due to the factors mentioned we may see jumps in some periods. CMMS software can be very useful to keep track of such pending work orders and help us ensure that they are closed or canceled as needed.
If maintenance backlog starts to increase, we must make sure to have a plan to start reducing it soon. An ever increasing maintenance backlog will soon result in major maintenance failures and a leave a maintenance department in total firefighting mode trying to keep up.
Take action to reduce maintenance backlog!
We must go through pending work orders to identify backlog causes. Find the most major causes of the backlog. Then we should take appropriate actions to reduce them.
If the maintenance department is overstretched, we can see if we can work with equipment vendors or outside contractors to get pending maintenance completed. We can use maintenance software to reschedule jobs as needed and close out redundant work orders.
Are other departments not releasing equipment and so delaying maintenance? We can work with them to set up a schedule to complete pending maintenance as well as future preventive maintenance.
Looking for CMMS/ maintenance software?
Get a web demo or download a 30-day trial of FastMaint CMMS software. See how you can use it to manage your maintenance backlog.
How to find & manage maintenance backlog in FastMaint:
The one page Statistics report available from the main screen or Home page (Cloud, Web edition) shows how much backlog you have and pending work orders from prior periods. Use the maintenance work order history report to locate only pending or past-due work orders so that you can complete or cancel them as needed.
Free FastMaint CMMS TrialAdditional Reading
- “5 maintenance backlog traps to avoid” from PlantServices magazine covers issues that can trip you up when trying to reduce maintenance backlog.
- “Maintenance Work Backlog Management” from Lifetime Reliability Solutions has some useful tips on classifying and managing backlog.
Essential Maintenance Metrics Every Planner Needs to Know
Get Free Guide