Essential Maintenance Metrics Every Planner Needs to Know
Get Free Guide
Every piece of equipment, machinery, and asset is a cog in the intricate machinery that propels a business forward. But what ensures that equipment operates at its optimum capacity, ensuring not only productivity but also safety and longevity? The answer lies in meticulous and strategic maintenance planning.
In the following sections, we will define what maintenance planning covers, discuss the relationship between planning and scheduling, outline the best maintenance planning principles, and show you how to double-check the health of your existing maintenance plans.
Let’s dive straight in.
What is maintenance planning?
Maintenance planning is a process by which maintenance managers and planners determine which assets or facilities need to be maintained, what should be the frequency of maintenance work, and which parts, materials, and tools will be needed to complete the job.
The ultimate goal of maintenance planning is to have a structured process that helps you keep assets in proper working condition while balancing costs and maintenance resources.
The relationship between maintenance planning and maintenance scheduling
Though often used interchangeably, maintenance planning and scheduling are distinct yet complementary concepts, each playing a critical role in the holistic approach to effective maintenance management.
Maintenance planning, as we have discussed, involves identifying the “what” and “how” of the maintenance process. It defines which assets require maintenance, outlines the type of work that needs to be done, and estimates the required labor, materials, tools, and equipment. Planning is about laying down the foundation and preparing everything needed to execute maintenance work efficiently and safely.
On the other hand, maintenance scheduling deals with the “when” and “who”. It is a subsequent step that specifies times and dates to carry out the planned maintenance activities and assigns them to the appropriate personnel — while taking into account the workload and availability of their team and the production schedule.
An effective plan is only as good as its execution. The two should be closely integrated, with the planning providing a well-defined blueprint that the scheduling can follow systematically. This way, maintenance work can be planned — and executed — in a timely and effective manner.
7 maintenance planning best practices
Below is a list of key principles and actionable strategies to enhance the efficiency, reliability, and longevity of assets by establishing robust and polished maintenance planning protocols.
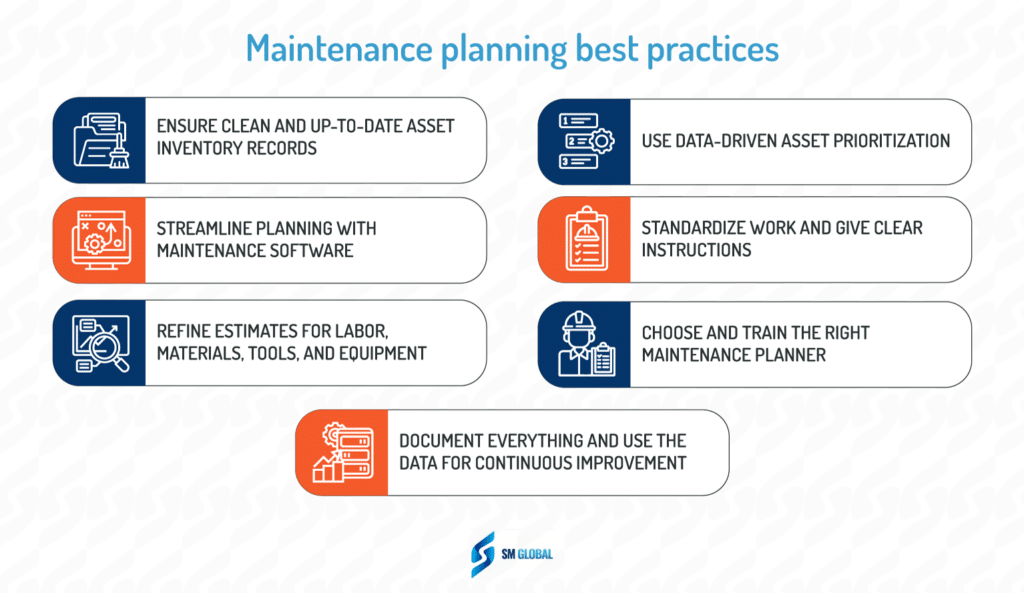
1. Ensure clean and up-to-date asset inventory records
An organized asset inventory ensures that maintenance planning is based on accurate, current data, which is essential for prioritizing tasks and allocating resources effectively. It also helps in identifying the assets that require immediate attention and those that can be scheduled for later, ensuring an optimized maintenance schedule.
Begin by conducting a comprehensive audit of all existing assets and equipment. Catalog each item, noting its specifications, current condition, and maintenance history. Eliminate obsolete records and update information to reflect the real-time status of each asset.
If you’re pressed for time, focus on critical assets and those that are on a preventive maintenance plan.
2. Use data-driven asset prioritization
Prioritizing assets allows maintenance managers to focus their efforts and resources on equipment that, if failed, would have the most significant impact on operations, safety, and productivity.
To ensure asset prioritization becomes a data-driven process, conduct:
- Asset categorization: Organize assets into categories based on their criticality. Use labels like high, medium, or low priority to simplify the process.
- Risk assessment: Evaluate each asset’s failure risks and the potential impact on operations. Consider factors like safety, operational downtime, and repair costs.
By classifying assets, maintenance teams can create customized maintenance schedules for specific assets or asset categories that are both efficient and cost-effective. The resources can be allocated where they are needed most, ensuring timely maintenance without over-allocating resources to less critical equipment.
3. Streamline planning with maintenance software
Using maintenance software is a pivotal step in improving the efficiency and accuracy of your maintenance planning as it streamlines the planning, tracking, and execution of all maintenance tasks.
Modern CMMS solutions offer invaluable insights through data analytics, aiding in informed decision-making. Maintenance managers can identify failure patterns and root causes, predict potential failures, and optimize maintenance plans and schedules accordingly.
Long story short, CMMS gives you the data you need to create effective maintenance plans — and the means to put them into action.
4. Standardize work and give clear instructions
Maintenance personnel should always have all the information they need to perform their tasks safely and effectively. Aside from including standard information about job location, duration, materials, and equipment, consider providing additional information such as:
- Standardized Operating Procedures: Develop easy-to-follow SOPs that include step-by-step instructions, equipment required, and expected duration for each task.
- Visual aids: Incorporate visual aids like diagrams or flow charts to make complex instructions more understandable and accessible.
- Accessibility: Ensure that instructions are easily accessible to all technicians, preferably through digital platforms, for instant access to the most up-to-date version of the document.
By standardizing your processes, maintenance planners will have an easier time estimating how long specific tasks take to complete, and the exact resources needed to complete the job.
You can take this a step further by using SOPs to standardize the maintenance planning process itself. This speeds up the planning process and ensures consistency across the whole department, which is especially helpful when leading large maintenance teams with multiple planners.
5. Refine estimates for labor, materials, tools, and equipment
An integral part of maintenance planning involves precision in estimating the labor, materials, tools, and equipment required:
- Labor estimates: Evaluate the complexity of each task and assess the skill level and number of technicians needed. Consider past performance data to refine your estimates.
- Materials forecast: Analyze the materials required for each task, referring to historical data and manufacturer recommendations to estimate quantities needed.
- Tools & equipment allocation: Identify the tools required for each job. Confirm you actually have those tools on hand and consider the need for specialized equipment and safety gear.
Accurate estimations ensure that resources are allocated efficiently, tasks are completed safely and on time, and unexpected delays and costs are minimized.
6. Choose and train the right maintenance planner
A great maintenance planner should not only possess technical know-how but also organizational and analytical skills that allow them to develop well-rounded maintenance plans.
If you have an experienced planner, then you’re all set. If not, here’s what you can do:
- Look for individuals with a mix of technical knowledge and organizational skills. Being detail-oriented, analytical, and a good communicator are key traits of an effective planner.
- Provide comprehensive training tailored to the maintenance planning role, focusing on aspects like resource allocation, data analysis, and instruction writing.
- Make sure the person knows their way around any maintenance software you are using — how to pull reports, how to quickly find other asset/parts inventory information, how to use templates the speed up planning work, and so on.
Having the right maintenance planner underpins the success of the entire maintenance strategy. It ensures plans are not just technically sound but also strategically aligned with organizational goals.
7. Document everything and use the data for continuous improvement
Combining the aspects of continuous improvement with thorough documentation ensures that your maintenance planning evolves effectively while being well-recorded for analysis and future reference.
Here are some tips on how to put this into practice:
- Feedback loops: Create mechanisms to collect feedback on maintenance tasks. Use this data to identify areas for improvement and optimization.
- Performance metrics: Implement key performance indicators (KPIs) and metrics to measure the effectiveness and efficiency of maintenance activities.
- Digital documentation: Utilize digital tools like CMMS to record maintenance data in real-time, ensuring accurate, accessible, and comprehensive records.
- Reviews and updates: Regularly review and update maintenance plans and documentation based on technician feedback, performance data, cost projections, and other factors you decided to track.
As your maintenance plan expands, comprehensive and accurate documentation ensures that these changes are recorded, replicated, and used to improve future planning cycles.
How to check the health of your maintenance plans
Different maintenance programs have different reports. In FastMaint CMMS, the Work Order Analysis Report is very useful for checking if your maintenance planning is accurate and realistic.
The idea is to track the average number of days your team needs to complete assigned work orders. This “average” represents the difference between the work order Completed date and the original Planned date for each work order.
In other words, if a work order was planned for 1st July 2023 and was completed on 3rd July 2023, it took 3 days to complete it.
There are two warning signs you should be on the lookout for:
- Consistently high values for the average days needed to complete work orders
- Highly varying average days to complete work orders
1. Consistently high values for the average days needed to complete work orders
If your team is consistently closing out Work Orders past their due date, you should first make sure that the problem doesn’t hide inside your maintenance plan.
Here are a few things you should double-check:
- Tasks may actually take more time than estimated. If that is the case, here are some tips for improving your work order estimates.
- There are scheduling conflicts. The most common problems are having multiple maintenance tasks scheduled at the same time, maintenance technicians not being available or at a different location, and similar. In FastMaint, you can use the Availability Checking feature in the Work Order Planning Report before sending out work orders to identify such issues.
- Spare parts and supplies not available: Again, you can use the same Availability Checking feature to find such issues in advance. In addition, the system can also show you parts and supplies that need to be reordered.
2. Highly varying average time to complete work orders
If the average time to complete work orders varies hugely from week to week or month to month, it is a signal that your maintenance plan might be unbalanced. If so, check the following:
- There could be many big tasks scheduled at the same time in some periods of the year but not in other periods.
- Less skilled maintenance technicians will need more time to complete the same work when compared to their more experienced colleagues. Try to pair them together in the same shift to alleviate this problem.
- Spare parts shortages may be delaying work, increasing your mean time to repair. Review work order feedback and talk with technicians to identify this issue.
Now, imagine you open FastMaint and navigate to the Work Order Analysis Report that looks something like this:
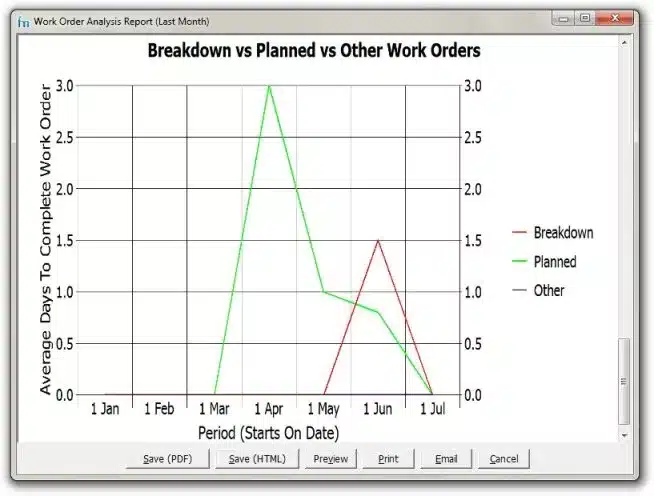
In this case, you would want to check what happened to planned work orders during the month of April — looking at the things we covered above — and act accordingly based on your findings.
Streamline maintenance planning and scheduling with FastMaint CMMS
From data capture and analysis to work planning, scheduling, and tracking, FastMaint offers maintenance teams all of the features they need to efficiently plan, schedule, and manage their maintenance work. Get a free trial today and start improving your maintenance operations while reducing inefficiencies and administrative burdens.
Essential Maintenance Metrics Every Planner Needs to Know
Get Free Guide