Essential Maintenance Metrics Every Planner Needs to Know
Get Free Guide
Maintaining optimal equipment performance is more crucial than ever. Enter proactive maintenance — a methodology that prioritizes preventing failures before they occur.
But what exactly is proactive maintenance, and how can organizations effectively integrate it into their operations?
Here we dig into the core principles of proactive maintenance. Get step-by-step guidance on implementing it to improve efficiency and reduce costly equipment downtime.
What is proactive maintenance?
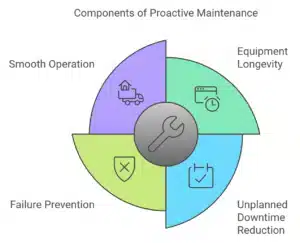
Proactive maintenance means taking a proactive approach to asset maintenance, reducing equipment failures and minimizing their impact. Instead of merely reacting to failures after they’ve occurred, as in reactive or corrective maintenance, proactive maintenance involves taking measures to foresee and address potential problems.
This approach seeks to keep equipment running more smoothly and for longer periods, reducing unplanned downtime and extending equipment lifespan.
Proactive maintenance strategies you can employ
Any maintenance strategy that you can use to jump in front of equipment issues and try to prevent them can be considered a proactive maintenance strategy. In that context, different forms of proactive maintenance include:
- Preventive Maintenance (PM): Involves scheduled maintenance tasks carried out at regular intervals, such as cleaning, lubrication, inspections, and minor replacements. The goal is to prevent unexpected equipment failures by maintaining them at routine times, irrespective of their current condition.
- Condition-Based Maintenance (CBM): This strategy focuses on performing maintenance tasks when certain conditions are met. By monitoring the real-time condition of equipment via different sensors, maintenance is only conducted when there are noticeable changes or deteriorations, ensuring that resources are used only when necessary.
- Predictive Maintenance (PdM): Represents a step beyond CBM. PdM works by continuously analyzing the data coming from condition-monitoring sensors and other inputs. That data is used to create predictive algorithms that can spot trends and predict equipment failures, allowing maintenance teams to efficiently (re)organize internal resources and perform actions just in time to prevent those failures.
- Reliability-Centered Maintenance (RCM): This approach uses a structured framework to determine the most efficient, safe, and cost-effective way to maintain an asset. It integrates preventive and predictive maintenance techniques based on the reliability and criticality of each piece of equipment.
Preventive vs proactive maintenance dilemma
Preventive maintenance will try to perform repairs or parts replacement based on a maintenance schedule. For example, an inspection every Thursday, an oil change every two weeks, a gasket change every 1000 run-hours, and so on.
You will find some articles that define proactive maintenance as its own strategy, focused on finding the root causes behind equipment failures and taking proactive actions to address them.
For instance, you may identify poor quality lubricant as one cause of failure. Or a technician not seating a gasket properly as another failure cause, and so on. The idea is that fixing these issues, alongside performing regular preventive maintenance tasks. This will significantly cut your costs and unplanned downtime in the long run.
While there is not a clear consensus in the maintenance industry, we think of proactive maintenance as your general approach to asset management. Take proactive steps to predict and prevent equipment failures.
There are many different maintenance strategies and techniques we can employ to do that, root cause analysis being just one of them.
Make proactive changes based on the root cause of equipment failure
Equipment failures happen for a wide variety of different reasons. Still, some are more common than others. We recommend to start your investigations by looking at the following issues:
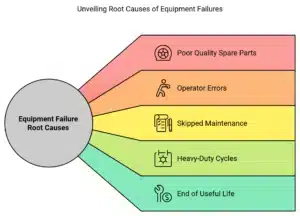
- Poor quality spare parts or supplies: Do you see many breakdowns due to part failures? Look at work order feedback inside your maintenance system. See if the same spare parts & supplies issues are mentioned frequently and cross-reference that with the vendors that provide them.
- Operator errors or misuse: Operator mistakes are a common reason behind equipment failures. Instruct techs to highlight these cases while they are closing out their work orders. If you notice a trend, train operators on how to use equipment to avoid such failures.
- Is recommended maintenance being skipped? When the maintenance team is over-extended, some maintenance tasks will get delayed, if not outright skipped. It is time for a change if you find many work orders pending or canceled. Start by making a clear process for task prioritization.
- Unusual heavy-duty cycles: Peak usage during a busy season can lead to an increase in equipment breakdowns or quality problems. Check the historical failure reports. Cyclical failure patterns often point to seasonal loads. Be more aggressive with preventive maintenance during these peak periods.
- Equipment at the end of its useful life: Sum up maintenance costs, downtime losses, and quality issues. At some point, it is more cost-effective to replace an asset than to continue repairing it. Look into your task and equipment history reports. Check how often a specific asset (or the whole class of equipment, like HVAC units) is failing. See how much is that costing you in terms of parts, labor, and downtime.
After you find out the root cause behind specific equipment failures, it is going to be much easier to decide which proactive maintenance action offers the best way to solve it.
The solutions can vary from increasing the volume of preventive maintenance work or implementing condition monitoring sensors to implementing specific workflow changes like writing standardized operating procedures or switching to a different spare parts vendor.
How to transition from reactive maintenance to being proactive
The transition from reactive to proactive maintenance requires a combination of cultural, organizational, and technological shifts. Here are some important tips to guide this transition.
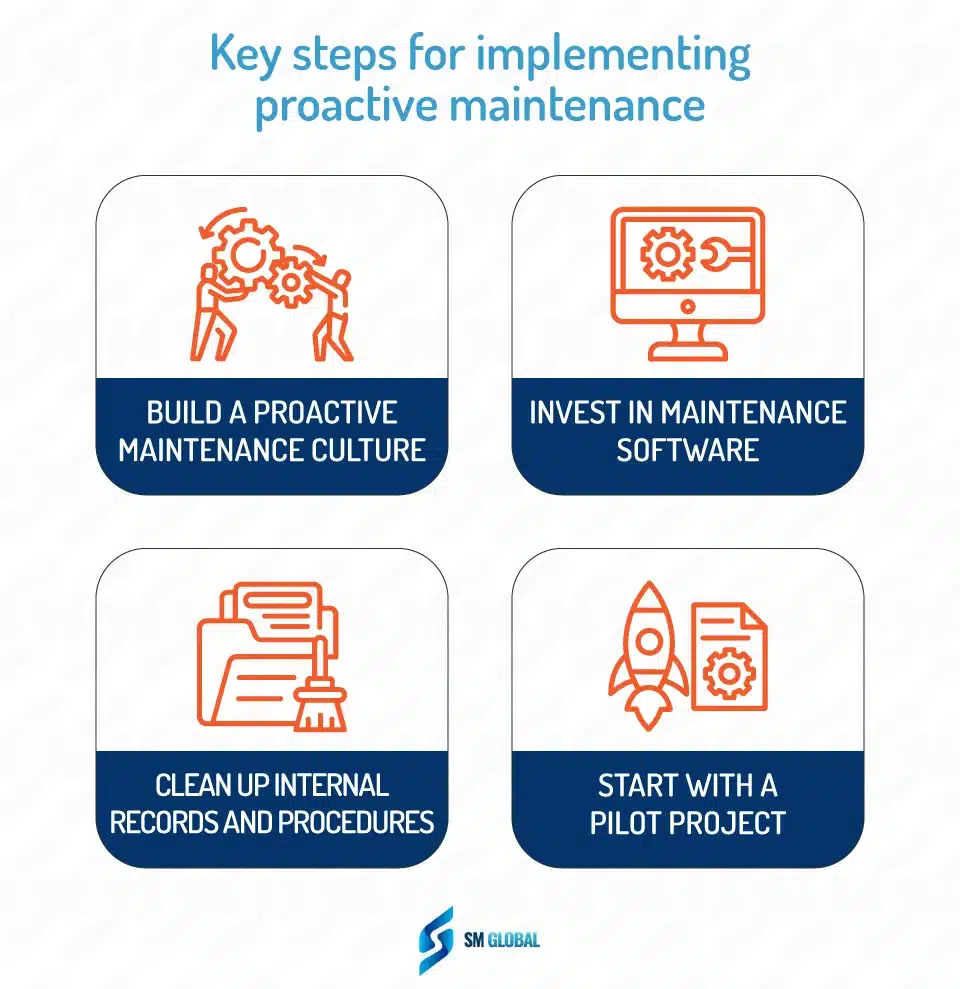
Build a proactive maintenance culture
The first step in any significant change is cultivating the right mindset. If your maintenance team is completely stuck in the reactive mode, it will take some time to change their perspective.
Engage and educate your team about the benefits of proactive maintenance. Some training sessions, workshops, and open forums can foster understanding and commitment. Celebrate the small victories and milestones to highlight positive changes and keep the momentum going.
Invest in maintenance software
Computerized Maintenance Management Software can be a game-changer. It helps in planning, tracking, and managing maintenance activities, while also providing valuable data analytics. By digitalizing your maintenance processes, you can access real-time information, automatically trigger routine checks, and have better control over your MRO inventory.
Many organizations, when they decide to move from reactive to proactive maintenance, will start the process by implementing a CMMS system, allowing them to plan, schedule, and track all of the preventive work they will be doing.
Start small, with a focus on critical assets
This transition can’t happen overnight. It’s too complex and overwhelming, especially for large organizations with big maintenance teams.
Start small. Select two or three critical assets — preferably those whose failure have the most significant impact on operations — and put them on a preventive maintenance plan. Use this pilot project to train technicians and start building out new workflows.
By focusing on these key assets first, you’ll be able to see the benefits of proactive maintenance more quickly and build a strong case for expanding the approach to other assets.
Set strong foundations
Before you go all-in on proactive maintenance, it’s time to clean house. Perform a quick SOP, parts inventory, and asset audits to set a baseline and know what exactly you are working with. It’s going to be hard to perform preventive maintenance actions if you are missing tools and parts and can’t locate all of your assets.
It’s also a good idea to write down some general numbers about costs, downtime, and equipment failures so you can easily compare them a few months into the pilot program.
Get ahead of equipment issues with FastMaint CMMS
Proactive maintenance is no longer a luxury but a necessity for businesses aiming for long-term success and sustainability. Transitioning from a reactive approach may initially seem challenging, but with the right mindset, tools, and strategies, measurable improvements can be seen in just a few months.
Simplify this transition to proactive maintenance by implementing FastMaint. It’s an easy-to-use maintenance management software that helps you plan, organize, and track all of your maintenance resources.
Free CMMS Software Selection GuideEssential Maintenance Metrics Every Planner Needs to Know
Get Free Guide