Essential Maintenance Metrics Every Planner Needs to Know
Get Free Guide
The Hidden Costs Of Maintenance Parts Management
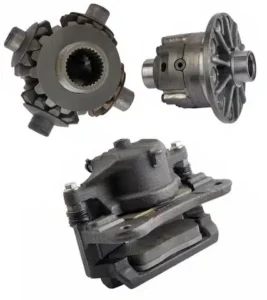
Managing maintenance parts and supplies can be hard. This become a harder still if we have many types of equipment to maintain.
Each type of equipment will have its own unique set of parts and supplies for corrective and preventive maintenance. Some of our customers have several thousand different types of parts. Imagine trying to keep track of each type as well as how many you have so that you can complete maintenance work as needed!
But that’s just part of the story…
Equipment spares can cost a lot and add a lot to the maintenance budget.
In addition keeping enough stock on hand of many types parts & supplies will also add to the maintenance budget.
How Can one Improve Maintenance Spare Parts Management
1. Identify Parts & Supplies Used
Identify the parts & supplies required for different maintenance tasks. Try to estimate items and amounts needed over the next few months based on the equipment preventive maintenance schedules. This will help manage inventory needs and costs better. Holding inventory we do not need for several months adds to costs.
2. Use Just In Time Inventory Management
Depending on our suppliers (vendors) we can explore use of just in time inventory. It means we order & get parts just before starting maintenance jobs.
The trick is to avoid job delays because parts are not available when we need them. Depending on the suppliers the costs for certain parts may be much higher if we want just in time inventory. But this is often less than the costs due to lost production or cascading equipment failures because we have to wait for parts to complete maintenance!
3. Use Reliable Suppliers
Poor quality parts can result in early failures and more maintenance work. Use maintenance records to identify suppliers of quality parts. Corporate purchasing requirements may dictate the choice of suppliers. Still it can be possible to work with the purchase department especially if we have statistics about vendor quality & reliability.
Just think about it.
To implement these tips you need to be able to collect and analyze a lot of data. Ideally this can be done with maintenance management software.
How Maintenance Management Software Can Help
Experts estimate that organizations can save between 5-10% on their yearly spare parts inventory costs with a maintenance management program aka CMMS software. Proper use of CMMS software reports and inventory management features can help reduce inventory carrying costs as well work order completion time.
For example with CMMS software we:
1. Will have parts usage and inventory reports.
Look for parts & supplies usage history reports. With them we can better track inventory purchase & consumption over time. We will also get an idea of the costs and how much of our maintenance budget needs to be assigned for spares & supplies.
Having too small a budget for spare parts & supplies means that work orders get delayed since there will not be parts on hand.
Having too large a budget for parts & supplies means that there is too much inventory on hand. In addition, many parts & supplies may expire or no longer be needed. Plus we have to make space for them and keep track of them. This money could be better spent elsewhere!
2. Find out how many parts of each type we will need for preventive maintenance in the future.
Use planning reports to calculate parts and quantities needed for future periods. This can help one apply for volume discounts when ordering spares and supplies. In addition it will make it easier to use just in time inventory since we will know in advance some of the items needed.
3. Specify reorder levels when to restock items.
The maintenance management software can warn us when each part or spare falls below reorder levels. This means keeping less inventory on hand. It saves costs in purchase & storage. Being able to set reorder levels is one of our customer’s favorite features in FastMaint CMMS. Parts that fall below reorder levels get marked in red. They can see at a glance what is running low.
4. Can associate parts & supplies with equipment.
When equipment is retired we will be able to identify parts that can be disposed since they are no longer needed (see “Using Maintenance Software To Identify Equipment Needing Replacement“). This reduces the inventory carrying cost. We can free up money for the maintenance budget by selling or returning items that are no longer needed for maintenance.
5. Can review work orders reports to identify parts that fail frequently.
Look at work order reports. Are we doing the same maintenance work again and again? Are maintenance technicians reporting parts related problems in the work order feedback? See if it was due to poor quality parts. Tag good & bad suppliers.
Looking For CMMS Software?
Not happy with your current maintenance program? Want to see if another product can work better for you? Get an online demo or download a free trial of FastMaint CMMS software. FastMaint can help you use the tips here to improve spares & supplies management as well as equipment maintenance .
Free FastMaint CMMS TrialEssential Maintenance Metrics Every Planner Needs to Know
Get Free Guide