Energy Transition Company Sees Major Benefits from Use of Maintenance Management Software
Frank Seipel, an engineer at Vertex Energy, says his company’s use of FastMaint has had a real positive effect on its efficiency over the years.
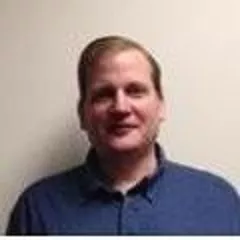
So it’s little wonder that Vertex Energy has been using FastMaint for more than 11 years now, and has also installed it in two different company locations.
“FastMaint improves communications over a paper system and it improves tracking of asset performance,” Seipel said.
How FastMaint Works:
FastMaint is a standalone software program that is simple to install and that allows users to quickly and easily collect and track maintenance work requests.
The program can be utilized to perform inventory management, vendor management, purchasing and reordering, and to manage planned and unplanned jobs, among other things.
It offers multiple user accounts, customizable reports, an easy-to-use dashboard, task template creation, and fast setup among many other features.
Benefits Received by Vertex Energy:
Seipel revealed several benefits that Vertex Energy has received by using FastMaint to manage maintenance. Among those benefits were:
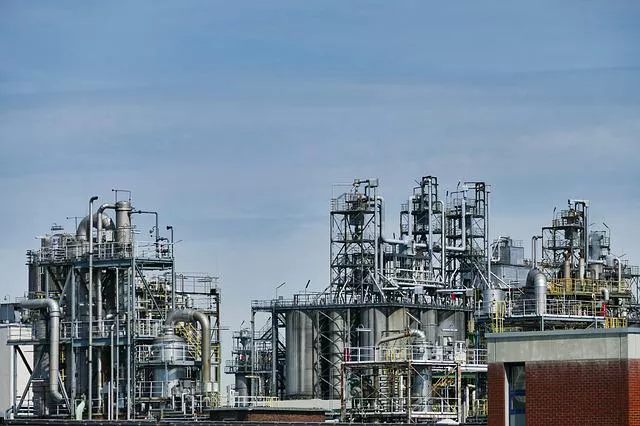
Ease of Use – FastMaint is very easy to install and use and that means little training is required. That means employees don’t lose time learning the software, instead they are able to get up to speed and take advantage of its many benefits right away.
Precision Scheduling – FastMaint handles ongoing preventative maintenance task scheduling on a daily, weekly, monthly, yearly basis. This helps ensure important maintenance is never overlooked or forgotten.
Inventory Tracking – FastMaint tracks parts inventory so users don’t have to worry about unexpected shortages that can disrupt a business’s operations.
Seamless Communication – FastMaint allows users to send emails upon completion of work orders with just one click.
Vendor Accessibility – FastMaint keeps track of all vendor contact information so that vendors can easily be contacted when needed.
Responsive Support – FastMaint support personnel are quick to respond to questions. FastMaint also values the opinions of its customers. In fact, Seipel says it has consistently added requested features over the years and has assisted his company whenever they have had any issues.
The Bottom Line …
Vertex Energy, which is based in Houston and which is focused on the production and distribution of conventional and alternative fuels, says it has benefited significantly from its use of FastMaint.
The company primarily uses FastMaint to track its recycling of used motor oil (crankcase oil) for Valvoline and other oil change shops.
Seipel says at his company, “Fast Maintenance improves communications over paper system, and improves tracking of asset performance, such as number of work orders, parts consumed, aids in maintaining critical spares, and tracking completion times of work orders/open work orders, and scheduling preventative maintenance checks.”
Concerning his company’s use of the software, Seipel says:
“I have been thoroughly satisfied with Fast Maintenance, it continues to meet our needs. We are now using it at two facilities (Marrero, Louisiana and Columbus, Ohio). It is simple to install and use and we have been pleased with the customer support and updates received over the years. We’ve been using it around a decade at (my) site.”
Seipel went on to say: “I would highly recommend it to others for use at their plants.”